Taking It to the Next Level
ARUP Attains Hard-Earned ISO Accreditation
Earning this standard gives ARUP the opportunity “not only to ‘study for the exam,’ but also to ‘learn for life,’” said Frank Schneider, MD, FCAP, and chair of the College of American Pathologists (CAP) 15189 Committee. Two years of work in examining and sharpening processes at ARUP— performed closely with CAP advisors—resulted in this internationally recognized standard for laboratories.

The accreditation essentially recognizes that ARUP is extremely competent and has operational systems in place that back up that competency. “In clinical lab accreditation, this is a fairly new program [since 2008 from CAP]—on the cutting edge—and we’re one of the largest labs to reach this stage,” said Janice Pinterics, ARUP quality manager. “Before this, the accreditation had not gone to a laboratory of our size and high level of complexity.”
This is a significant achievement, setting ARUP apart from other large organizations. Pinterics, along with Jonathan Carr, director of Compliance, Quality, Privacy and Risk, and an ISO Steering Committee of 15 or so individuals from multiple departments (including Technical Operations, Compliance & Quality Systems, Finance, Purchasing, Medical Directorship, Human Services) spearheaded several months of coordinated changes that earned the lab this honor.
Achieving this status just further validates the value that everyone here places on the work that they do for patients. They want to do it with the highest quality possible.”
Dr. Ron Weiss, ISO Steering Committee member and ARUP former Chief Operating Officer
The serious work began in August 2014, when ISO assessors performed a “gap assessment” at ARUP to find areas where the laboratory would need to make changes and integrate systems to achieve ISO 15189 accreditation.
Hammering things into place as an organization, bringing six laboratory divisions together to communicate about best practices, and integrating a new system took perseverance and dedication. “We were always good at identifying problems,” notes Carr, “But now we can be more effective at stopping them from repeating. Now our processes require us to prove to ourselves that the same mistake won’t happen again.”
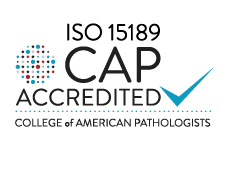
“It’s a culture of identifying process improvements. We’re getting better at sharing best practices and identifying where multiple labs may be struggling with the same types of issues,” says Jonathan Carr (left), who worked closely with ARUP colleagues Janice Pinterics (center), Dr. Ron Weiss (right), and others on the ISO Steering Committee in attaining ISO 15189 accreditation
Four Different Perspectives on the ISO Accreditation Process
Perspective Jonathan Carr, 
ARUP’s Director of Quality, Privacy, and Risk
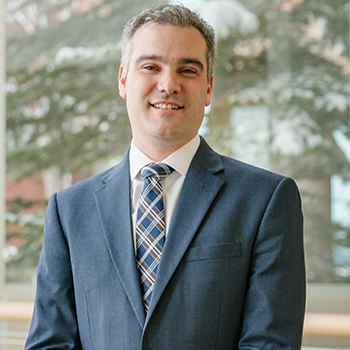
What does ISO 15189 accreditation mean for ARUP?
The accreditation not only shows our commitment to quality and identifying errors, but also to assuring we’ve corrected them effectively (closed the loop), identified a problem, its cause, and its corrective action, and then evaluated whether the corrective action is effective. We are also improving ways for our various lab sections to learn from each other as corrective actions are implemented.
What’s an example of something that has changed with ISO accreditation?
We have made an effort to enhance the culture of identifying process improvements, not just reacting to human error. If we find that someone is not following every step of the official written process, our ISO 15189 processes force us to ask why a step was omitted. But in the process established by ISO accreditation, we ask why it happened, and there is room for communication—for learning how to make the system better. The organization takes appropriate responsibility for the error and identifies how the system should be improved, in addition to any individual accountability.
Implementing ISO 15189 helps us continue to learn why things happen, and make appropriate changes as a result.
Perspective Janice Pinterics, 
ARUP Quality Manager
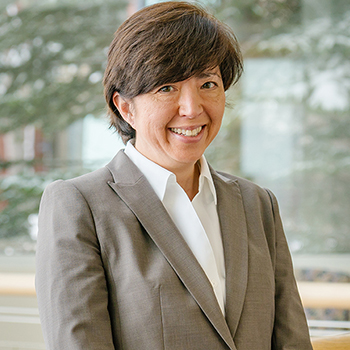
What was one of the major changes?
Previously, we used a database to write up any problems and what actions we took to fix them, then cases were closed without review. For ISO accreditation, we significantly reconfigured the system to harmonize our method of investigating problems, and there was training for everyone using it. The change required buy-in from multiple areas that were previously relatively independent—all six lab divisions worked with the CRM Salesforce team, IT, and CQS. We had to work out any issues in the new system and agree upon a harmonized approach for investigations and reviews.
How did ISO accreditation sharpen ARUP’s already existing high quality?
I think the accreditation presents an advantage for ARUP in a few different ways: it promotes standardization and harmonization as an organization. Additionally, ISO really wants to give technologists a voice to empower them to take a part in redesigning our process with the shared goal of improving patient care. Reaching a consensus for the required changes within a large organization and empowering our employees is a very unifying event.
What has changed?
In the past, ARUP was good at containing problems—we have always been very responsive and able to correct and contain the immediate issues; frequently, this would involve retraining an individual on a procedure that wasn’t followed. But because doing so takes a lot of time and our labs are extremely busy, we didn’t consistently go back to find and address the true underlying root cause. ISO is saying don’t just retrain a person on a procedure; we want to hear back on whether the procedure was clear, whether the training was adequate, and whether our process is flawed. When we ask these more difficult questions and get to the real root causes and fix them, it allows us to continually improve processes.
Perspective Amy Pennock, MS, 
ISO 15189 Lead Assessor, College of American Pathologists (CAP)
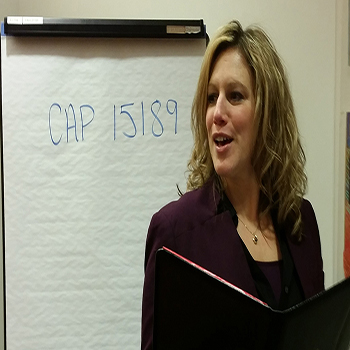
What catches your eye about ARUP since it achieved ISO 15189 status?
ARUP is now truly empowering the staff at all levels. As an employee, that means changing the way you think about doing your job every day. Instead of thinking, “I’ll come in and do my work and leave at the end of the day,” ARUP employees are now taking a broader view of their work area and the surrounding areas, then vocalizing their ideas and getting involved in driving improvement. It’s important that staff be heard and truly listened to, and that action is taken. That’s now taking place at ARUP.
How is ARUP unique in achieving this new status?
Given the test menu that ARUP offers, it is among the largest organizations to achieve ISO 15189-accredited status. It’s impressive that an organization with so many labs has been able to unify those sections with best practices and effective ways of sharing information. From an assessor’s perspective, I see greater communication throughout the organization—across departments, and across leadership at local and across executive management.
What’s the significance of ARUP having achieved the status?
Seeing ARUP and the journey it has been on to achieve accreditation—the dedication of staff at all levels, from management to bench-level—demonstrates a commitment to quality testing, and, most importantly, to patient care. It has been exciting to observe the evolution of ARUP’s quality management system.
Perspective Ronald L. Weiss, MD, MBA, 
ARUP ISO Steering Committee
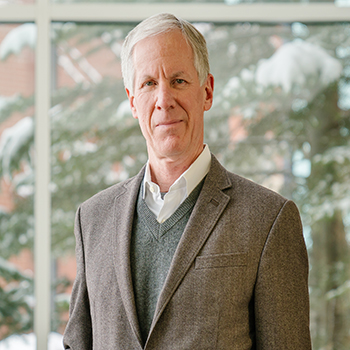
A member of the ISO Steering Committee at ARUP and professor of pathology at University of Utah, Ron Weiss, MD, MBA, is ARUP’s former president/chief operating officer and is now a senior hematopathology consultant.
What does ISO 15189 accreditation mean to you?
I think ARUP’s history has always been focused on service quality and a commitment to excellence in healthcare. Achieving this status just further validates the value that everyone here places on the work that they do for patients. They want to do it with the highest quality possible.
You were a member of the ISO Steering Committee, which numbered about 15 individuals who contributed from various departments to the two-year process of making adjustments at ARUP to achieve ISO 15189 accreditation. What brought you to the committee?
I was asked to join, in part to represent the medical directors’ group with Dr. Chris Lehman [comedical director, University Hospitals and Clinics Clinical Laboratory], who has experience through the College of American Pathologists with the ISO process. The goal was to determine how best to message to our fellow medical directors how their lives would be impacted, and to encourage them and be a resource as they activated those standards. Given my long history at ARUP and experience in the quality program, I was interested in the opportunity to participate.
What else is exciting about the accreditation?
It was gratifying to see this process play itself out, and to see the commitment not only of the Steering Committee, but everyone at ARUP. In a sense, I was not surprised that we ended up with ISO accreditation. As with any process, there were points of adjustment, but there was always commitment from the staff at ARUP to make this happen.